DOWNTIME is the very apt acronym used in “Identifying and Eliminating the 8 Forms of Waste in Manufacturing” to break down the major sources of manufacturing waste. Written by Alexander Federici of Lean Transformations and recently posted on CMTC (AKA California’s Manufacturing Network), the blog details the major causes and solutions for waste ranging from D (Defects) to E (Excessive Processing).
How can a visual intelligence tool like Leela Platform address these issues? Let’s take a look:
D (Defects) – While visual intelligence is designed for process detection, defect detection is best solved by a more established type of AI-infused software dedicated to product inspection. Yet, as we detailed in a recent blog post, solutions such as Leela Platform can augment product inspection by flagging issues that might otherwise not be recorded. (One of our customers, for example, used Leela to discover that assembly technicians were taking too long to attach a part that turned out to be mis-sized.) In short, video intelligence can act as an always-on backstop to more purpose-built quality control detectors.
O (Overproduction) – Visual intelligence can offer a ground truth check for overproduction trends that are usually identified first in other manufacturing software. The software is also adept at analyzing staff deployment, giving manufacturers the information they need to quickly reassign workers to other tasks when production has overstepped demand.
W (Waiting) – This is where visual intelligence solutions really shine: revealing when and where line employees are waiting around. Not only can the software spot relatively minor bottlenecks that increase wasted labor over time, it can also analyze the entire production process to help managers quickly identify the cause and potential solutions. Delays caused by excessive waiting are often missed by the human eye or IIoT sensor analytics.
N (Non-Utilized Skills and Creativity) – Federici breaks this often-overlooked waste category down into a lack of engagement, empowerment, and development (training) among employees, as well as the mis-deployment of workers to tasks. Visual intelligence can help address all four challenges. When manufacturers share the Leela Viewer dashboard of production metrics charts throughout the organization, frontline operators are more likely to become engaged in the process. By inviting them to share their own insights into production improvements, they tend to feel more empowered to improve their work process, and by using Leela to record and share best practices in training videos, operators can improve their skills. Finally, by analyzing productivity, managers can more effectively reassign operators to find the best match for their strengths.
T (Transportation) – Visual intelligence supplies the deeper visibility into operations to help quickly adjust production processes in response to changes. These insights help to minimize the cost, delays, and potential damage involved in excessive transporting of “products, information, tools, materials, or people.” To reduce transportation waste, Federici recommends “identifying redundancies and inefficiencies” and “streamlining flow through routes, facility changes, processes, and scheduling.” Leela Platform can help with most of these tasks, and the software can also be applied to logistics operations.
I (Inventory Excess) – Federici breaks this out separately from Overproduction because excess inventory can also be caused by “ineffective forecasting, unforeseen materials shortages or shipping delays, over-purchasing, or problems meeting sales goals.” Most of these challenges fall under the purview of enterprise planning software. Yet Leela Platform, for example, provides an API that enables planners to add production trends into the forecasting mix for more timely observations.
M (Motion) – Inefficient, dangerous, and ergonomically incorrect movements by human workers can lead to a host of problems ranging from low productivity to higher absenteeism, increased healthcare and insurance costs, and lower worker satisfaction and retention. Leela Platform is not currently optimized for ergonomics analysis, but it is optimized for analyzing human movements through pose detection. As a result, it can help flag potential problems in efficiency and safety, such as poorly placed tools and processes that require too much heavy lifting. One customer is using the software to identify and reduce the use of ladders to improve safety and health.
E (Excessive Processing) – Sometimes less is better in manufacturing. As raw materials, product designs, automation, regulations, and customer needs change, Federici recommends that manufacturers analyze their operations to identify wasteful steps that could be removed. Visual intelligence software provides the big picture view of operations to do the job.
CMTC’s “Identifying and Eliminating the 8 Forms of Waste in Manufacturing” offers many more interesting insights into the sources and solutions of waste. The bottom line, of course, is that wasting resources and labor leads directly to the biggest type of waste of all: money.
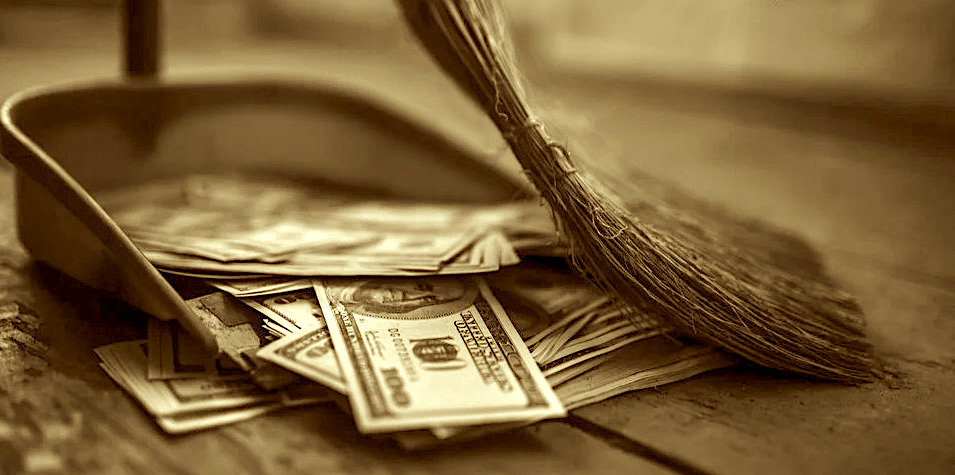