Cyrus Shaoul, CEO, Leela AI
I recently visited a precision job shop in western Massachusetts called Peerless Precision. I sat down with the owner, Kristin Carlson, who is also Chair of the Massachusetts Workforce Training Fund Advisory Board, who shared some of the realities of running a 20-person precision machining operation in the USA today. Many of the challenges she mentioned were familiar from discussions with other manufacturers: labor and supply shortages, the need to stay up to date with new technologies, and the continuing struggle to train and retain skilled technicians.
Two things became clear: First, Kristin goes above and beyond to create opportunities for her employees. Second, one of the ways she creates opportunities is to involve frontline technicians in continuous improvement, a practice that often helps improve retention and increase productivity. When I told Kristin about our vision of building a data conduit from our Leela Video Intelligence Platform to the frontline technicians, she was very supportive.
Kristin gave me a tour of the facility and introduced me to some of her team members. Kaitlyn, a machinist in her twenties, has been working at Peerless Precision for several years, first as an apprentice and then as an expert. She showed me the precision machining job she was working on and explained how measurements were built into the process to lower the defect rate. I told her about Leela Platform, and I asked her what she might like to use it for. Kaitlyn’s first choice would be to measure her consistency and see if she could find new ways to do things better and faster.
At first, her enthusiasm for bringing machine vision-based analytics into her workspace surprised me. Some workers are hesitant to be tracked on such a minute level, despite the facial blurring and other privacy controls that are found on most video analytics platforms for manufacturing. But then I thought about the fun that I have had figuring out how to do something better than before. Finding solutions to problems is part of human nature. Kaitlyn was eager to try new ways to solve her problems, and she sees AI as a way to provide her with the superpower of operational insight.
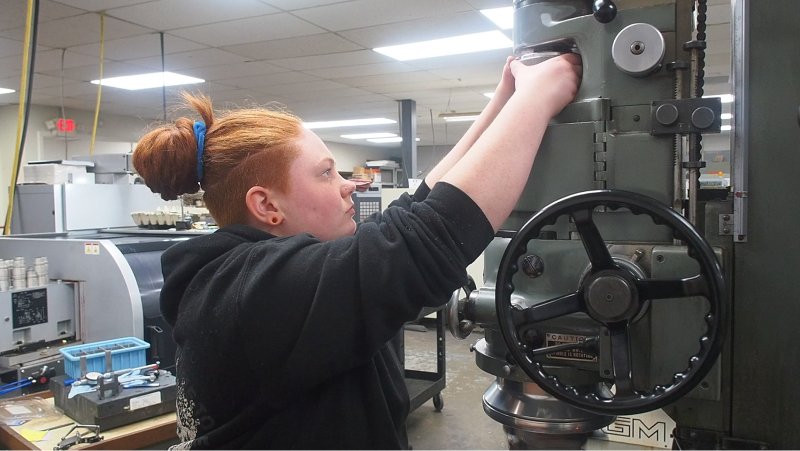
Learning from the experts: frontline technicians
Over the last 30 years, US manufacturers have been implementing variations on Kaizen practices for continuous improvement. Yet, one area where Kaizen is often underutilized is the involvement of frontline workers in improving products and processes. Whether managers are armed with time and motion studies, terabytes of IoT, MES, and ERP data, or their own experience and intuition, their plans for improvement will never achieve their potential without frontline input and support.
Manufacturers that actively pursue continuous improvement often establish analytics teams to sift through data and share insights. At their best, these are integrated with Kaizen quality circles, with representatives from different departments and – ideally – some frontline operators. Yet continuous improvement teams are often poorly integrated into daily operations. Typically, they have little power to make changes. More importantly, they usually lack sufficient input from frontline associates, who often have the best perspective into production issues.
Working the front line brings you closer to the process in ways that are impossible when you are only observing the operation or reviewing statistical data. Whether the task is washing dishes or assembling an aircraft engine, people naturally tend toward innovation. It could be a subtle change of posture, a better location to place a tool, or an idea for a slightly improved machine or part.
Veteran line associates are not the only untapped resource for continuous improvement. Even new employees can bring fresh insights. This is especially true in operations that rotate individuals between different tasks or educate workers on peripheral production processes upstream and downstream from their workstation.
Whether the task is washing dishes or assembling an aircraft engine, people naturally tend toward innovation.
Yet, the manufacturers that do seek insights from employees often struggle with the process. In some shops, workers may be hesitant to speak up for fear of being reprimanded. In other cases, the problems they encounter may not be easily reproducible, reducing their confidence in mentioning them.
Typically, however, line associates are happy to speak up. There is an inherent need in people to contribute. Motivations include the desire to improve personal safety, maintain pride in workmanship, avoid boredom, or improve one’s chances for advancement. Some may even act on the realization that they have a stake in improving the productivity of the company to ensure continued employment, and potentially, higher pay.
When workers do speak up, it is often difficult for managers to evaluate their feedback. This is usually because manufacturers lack sufficient visibility into operations to confirm observations, evaluate suggestions, or try out new techniques through measurable experiments.
Video intelligence as a shared resource
As we examined in a previous blog post, video intelligence software is a valuable new tool for analyzing manufacturing operations to improve productivity, quality, and safety, especially in high-touch facilities with a lot of human workers. Video intelligence can quickly identify bottlenecks and their root causes, as well as spot best practices and safety violations. All this data, including comparisons between similar workstations and different shifts, can lead to insights that improve productivity and reduce costly waste.
Armed with video intelligence, analysts are better able to evaluate observations and suggestions from the front line. Yet, if this operational data is viewed only by the analytics staff, there is a limit to its benefits.
Leela AI is dedicated to the proposal that video intelligence can only live up to its full potential if it is shared with everyone from the front office to the front line. With graphical, near real-time dashboard displays, everyone in the facility can gain operational visibility to confirm or reject hypotheses and steer a path toward innovation.
When this visual knowledge is liberated from the continuous improvement office and made available on the shop floor, frontline operators are better informed to make key observations and suggestions, and managers can more reliably evaluate their feedback. The dashboards offer a common framework for discussion, enabling drill-down on video segments to spot problems and identify best practices for training.
Transforming workplace culture is yet another way video intelligence can contribute to a manufacturer’s bottom line.
Some of our customers are placing monitors in work areas and break rooms so everyone can gather and see how their productivity and quality compares over time. In future releases, we plan to make it easier to spin out stripped-down, at-a-glance dashboards customized for each station that are viewable on a PC, phone or tablet.
With a measurable, visual record at their fingertips, frontline workers can speak up with more confidence. Perhaps a line associate has noticed a flaw in the production process or has an idea for a better solution. They can identify when and where the problems happen and acquire more insights into devising a solution that could avoid hours of costly delays.
Video intelligence can also be used to defend one’s performance. Frontline operators are sometimes cited as the source of problems that are actually caused by faulty parts, tools, or more commonly, processes. With video intelligence available to all, employees can better explain their actions in context with the facts.
I’ve learned a lot from my conversations with folks like Kaitlyn and Kristin. I’ve learned that the front line is ready to be augmented and empowered to take the lead on continuous improvement. Frontline empowerment leads to more interesting work, which in turn leads to higher motivation and retention. Transforming workplace culture is yet another way video intelligence can contribute to a manufacturer’s bottom line.