Given the profusion of digital technologies being pitched to manufacturers these days, it can be a challenge explaining Leela Platform. Many are still unfamiliar with the new category of video intelligence software for manufacturing productivity.
“So this is a surveillance system?”
“No, we don’t do surveillance, and you can blur faces for privacy. Our goal is to give you the data you need to boost quality and productivity through continuous improvement.”
“I get it, so this is a Manufacturing Execution System. We are not ready to get into all that.”
“Leela is not a MES, but something much simpler and easier to integrate. It’s called video intelligence.”
“Ah, so it’s a product inspection system.”
“Close, but it is not so much about product inspection as it is about process inspection.”
The eyes glaze over and I reach for my notes. Sometimes, my elevator pitch ends up in a free-fall to the basement. But when in doubt, there is always the blog.
It goes something like this: AI-enabled computer vision software first came to manufacturing space in the form of machine vision algorithms used to inspect materials and finished products. There are many capable product inspection platforms available that can detect defects, often at high speed and at the microscopic level.
Product inspection software enables manufacturers to ship higher quality products, thereby improving customer satisfaction and avoiding waste. Product inspection can reduce top-line waste from building unsellable products, which results in loss of revenue. It also covers bottom-line waste, including the raw materials wasted in a flawed product and the waste of labor and other operational costs used to build it.
Video intelligence software, such as our Leela Platform, can assist with product inspection at the macro level. Yet, it is primarily intended for something even more valuable: process inspection. With process inspection, the software can focus on inspecting the tasks and workflow by which a complex system builds the product. There are many opportunities for the software to flag defects in processes involving human operators, tools, and machines, and help to continuously improve them.
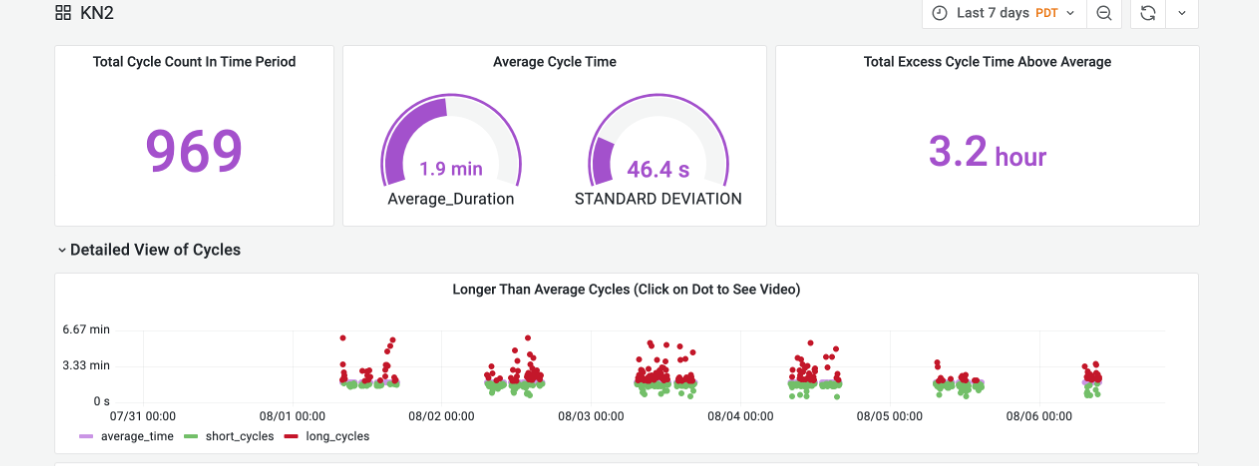
Product inspection is especially valuable in the manufacture of components. A single unidentified component defect has an amplifying effect, wasting the cumulative costs of every part used in the assembled product.
While process inspection can pay dividends in component manufacturing, it is even more valuable in evaluating the complex actions required to assemble finished products, especially in high touch operations where there are many human operators in the loop.
Video intelligence platforms can analyze the manufacturing process at every station on the line and compare activities with standard operating procedures. Leela Platform, for example, can identify operator practices that are sub-optimal or superior, thereby spotting problem areas and highlighting best practices for continuous improvement.
Video intelligence software further enables process inspection by identifying bottlenecks, such as slowdowns from operators who must wait for other work to complete. Leela Platform can also spot other forms of non-value-added time, such as when operators spend too much time walking around without a part or tool. The software can send a notification if non-value-added time crosses a threshold as a percentage of total assembly time.
Like product inspection, process inspection helps manufacturers avoid both top- and bottom-line waste. By inspecting processes and revealing ways to streamline operations, video intelligence platforms reduce the amount of time spent creating each product. This helps to avoid top-line waste resulting from having fewer high-quality products to sell, as well as the potentially larger waste from losing a customer due to delays.
Process inspection also helps to reduce bottom-line waste by minimizing the labor spent creating each product. Other types of bottom-line waste that can be identified by video intelligence software includes unsafe practices such as people who are not wearing a safety helmet in hazardous areas. Such safety lapses could otherwise harm workers and result in costly shutdowns, higher insurance premiums, and dissatisfied employees.
Hammering the point home
Although primarily designed for process inspection, video intelligence software can assist with product inspection on the macro level by ensuring that all the manufacturing steps were completed properly and in the right order. The software can also act as a backup for product inspection.
As an example, one of our customers recently used Leela Platform to identify a high level of defects in a particular pipe component. Leela does not use close-up image inspection, which would be challenging in the assembly process. Instead, the software noticed that workers were spending an average cycle time of four minutes to fasten a pipe to the product compared to the usual two minutes. Each pipe had to be hammered for several minutes until it fit.
If every pipe took this long to attach, an operator might have notified the manager that something was wrong. Yet since only some of the pipes were defective, and with multiple operators fitting the part, the delays had not been reported.
Leela Platform was able to quickly spot the problem and visually express the divergence via the Leela Viewer dashboard (see diagram above). As a result, the company determined the delays were caused by flaws from a single component supplier. They used that insight to save many hours of otherwise wasted labor.
Process inspection aided by Causal AI
Despite the similar goal of reducing waste via a combination of computer vision algorithms, process inspection is a very different task than product inspection. It quickly becomes too expensive and time-consuming to train Deep Learning algorithms to recognize the many SOPs within a video stream, especially if it spans an entire shift.
Yet many video analytics products for manufacturing productivity are essentially using extensions of the machine vision technology used for product inspection. Leela Platform currently stands alone in the manufacturing space as the only solution that adds causal AI processing to the industry standard Neural Network architecture.
Leela Platform’s causal AI algorithms, which are based on research done at MIT Artificial Intelligence Lab, go beyond recognizing patterns to comprehend concepts in context. The software can tease out complex processes within a workflow that can be captured, timed, and analyzed. This same causal awareness also greatly reduces the amount of training time required to learn each task. In other words, Leela is designed from scratch for inspecting processes.
There – now if I can just get that down to 100 words or less, I can go back to the elevator.